Eliminate Costly Component Out Of Pocket Defect Condition during Semiconductor IC Transport/Handling
Rich Rochford, Electronic Combat Solutions, BAE Systems Nashua, NH Richard.Rochford@baesystems.com
Craig Blanchette, Electronic Combat Solutions BAE Systems Nashua, NH Craig.Blanchette@baesystems.com
Abstract—High value devices used in microwave modules and other microelectronic assemblies have become increasingly thin and susceptible to “Component Out Of Pocket” (COOP) conditions that may occur during packaging, shipping, and customer handling. This defect condition is especially problematic for automated assembly which strives to be touch-free and efficient with orderly device presentation.
COOP is a major contributor to “Cost Of Poor Quality” (COPQ) within the business. A funded study into COOP conditions was conducted and multiple root causes were identified.
It was discovered that traditional “waffle packs” have mechanical issues related to looser flatness tolerances with respect to the tray and lid. The addition of a standard clip further contributes to the issue, both of which are key root causes of the costly “Component Out Of Pocket” (COOP) condition.
A novel Lid-Clip System (LCS2) was engineered to compensate for those mechanical issues, bringing robust captivation and preservation of devices in tray pockets. Static dissipative material for lid and clip was selected to provide unparalleled ESD Class 000 protection for high value devices with the lowest voltage susceptibility thresholds.
INTRODUCTION
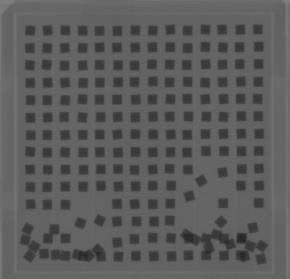
This paper describes the multiple root causes of the “Component Out Of Pocket” (COOP) (Fig. 1) defect condition in waffle packs that has persisted in the microelectronics industry for decades, complicating the task of achieving zero defects and driving manufacturing costs. Military aerospace and commercial manufacturers alike, worldwide are incurring unnecessary costs in the form of component damage, component scrap, and the non-value added labor associated with “fixing” induced waffle pack defects. Innovation in transportation, handling, preservation, and storage for semiconductor ICs has been lacking.
This is important because semiconductor devices in particular are costly and the additional assembly labor and equipment down time is a cost driver in manufacturing operations that use components with thickness of 0.010-inch and less. These components are particularly susceptible to this defect condition.
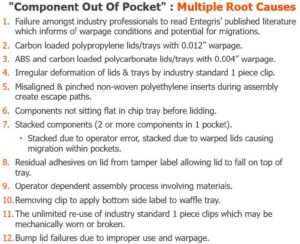
II.CHARACTERIZATION / ROOT CAUSES
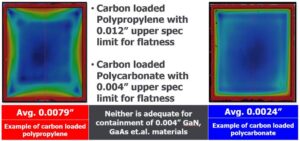
Multiple causes of COOP defects have been identified (Fig. 2). Many semiconductor industry professionals have failed to recognize the implications of published flatness specifications [1] associated with injection molded trays and lids (i.e., 0.012-inch carbon loaded polypropylene, 0.004-inch carbon loaded polycarbonate) (Fig. 3). For a thin GaAs die, that leaves plenty of egress for escape. Consider the tolerance stack up when selecting from standard lids and trays as it could be as high as 0.024-inch and 0.008-inch for poly-propylene and polycarbonate, respectively. Standard clips also impart deflection of lid and tray material due to the design as shown in (Fig. 4).
|
![]() |
![]() |
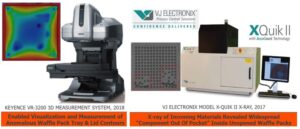
For decades, end users and suppliers of components in waffle packs have been pointing fingers, casting blame on one another for migrated components. Keyence VR-3200 3D Scanner [2] was key to visualizing and measuring the flatness tolerances that led to the mechanical issues that cause COOP (Fig. 5). With the advent of an x-ray counter system by VJ Electronix model XQuik II [3] (Fig. 5) developed for BAE Systems
in 2017, specifically designed to count components in sealed waffle packs at the receiving inspection level, we have definitively proven that COOP occurs both at supplier sites and during transit, well before end users have the opportunity to open waffle packs.
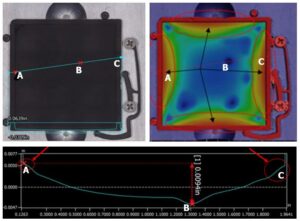
Principally, flatness tolerances of the various materials used in the manufacture of waffle pack trays and lids were visualized and measured using equipment shown in (Fig 5). Semiconductor industry component suppliers are typically unaware they are shipping components out of pocket because few employ x-ray systems to validate the effectiveness of their final packaging operation. While there is plenty of blame to be shared for COOP, including by end users, we now have a clearer understanding of the mechanical issues which top the list of multiple root causes.
Figure 6 shows dark orange locations A and C on inside of cover that act as standoffs when contacting top of tray thus allowing components to migrate under the blue locations that measure up to a 0.0094-inch gap.
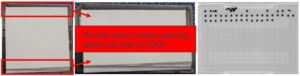
Another prevalent cause of COOP is the misalignment of loose inserts that leads to pinching of inserts used for the waffle pack assembly process (Fig. 7). One misconceptions is that loose inserts prevent COOP however, our research has shown it can actually contribute to it, as when inserts are misaligned or pinched which is frequently the case. Pinched inserts can be evident along edge in between tray and lid.
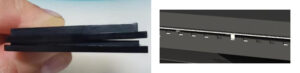
The risk of device damage is inherent to components when working with loaded waffle packs with that risk amplified for components ≤0.010-inch thick. The risk of COOP is present when clips are attached and removed, because the lids are essentially unsecured and waffle packs are being tilted to some extent; the lid can pop up on one side when unequal pressure is applied by operator to opposite side of waffle pack. That condition combined with the slightest vibration can cause COOP. It is at this stage of the packing and unpacking process where components are also at significant risk for migration (Fig. 8).
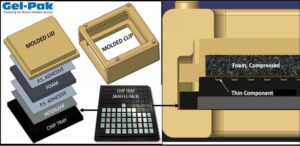
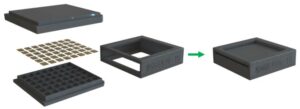
In response to the multiple deficiencies identified in the most commonly used bare die packaging (i.e., waffle pack/chip tray), a novel Lid-Clip System (LCS2) was engineered to pair with these warped pocketed trays to ensure optimal component preservation through the effective gasketing in each and every pocket in order to establish a new industry best practice and defect free transport/handling solution. LCS2 represents an important new option for the mitigation of “COOP”. Our solution is an enhanced lid comprised of low outgassing, static dissipative, low density polyurethane foam and industry-approved interleaf material assembled into a static dissipative injection molded lid using silicone free pressure sensitive adhesive (Fig 9). This is combined with a novel clip design (Fig 9 and Fig 10) which uniformly compresses the lid around its full perimeter, ensuring intimate contact of the entire interleaf against the warped waffle tray surface (Fig 11).
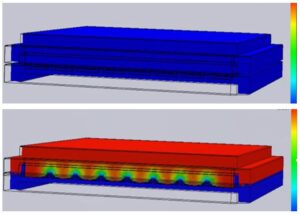
Static dissipative material for the injection molded lid and clip was selected and tested per ANSI/ESD S11.11 to provide ESD Class 000 protection for high value devices with the lowest voltage susceptibility thresholds.
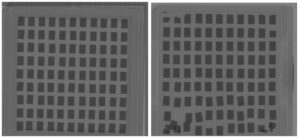
Efficacy of the Lid-Clip System has been demon-strated through rigorous drop testing of 0.002-inch GaN devices from 34 inches using x-ray to verify containment or the absence of COOP condition (Fig. 12). Ten unique novel lids and novel clips were tested and dropped a total of 10 times each for 100 total drops with no detected COOP (Fig. 9). When the standard industry clip was substituted for the new innovative clip, COOP occurred (Fig. 12) demonstrating need for the novel clip.
Overall, this novel Lid-Clip System solves for the costly “Component Out Of Pocket” condition for all sized components but especially for ultra thin components ≤0.010-inch. This system also reduce non-value added Supplier Corrective Action Requests/Return Material Authorizations. The Lid-Clip System has tremendous potential to curb millions of dollars in waste and improve component process efficiencies worldwide.
REFERENCES
[1] Entegris website Tray Wizard (entegris.com)
[2] Keyence website Models: Wide-Area 3D Measurement System | KEYENCE America Ryan Mathes
[3] X-Ray – VJ Electronix, Robert Kerwin
[4] Forgione Engineering, Matteo Forgione